The Function of Welding Assessment in Stopping Failings and Enhancing the Longevity of Welded Frameworks and Elements
Welding evaluation is a vital element in the lifecycle of welded frameworks, serving as a positive step versus prospective failings that can jeopardize security and capability. The application of varied inspection strategies not only ensures compliance with market standards however also cultivates a durable society of high quality guarantee.
Value of Welding Examination
Welding evaluation works as a vital guard in the integrity of welded frameworks, guaranteeing that they meet strict safety and high quality requirements. The importance of this procedure can not be overstated, as it plays an important duty in recognizing possible concerns before they rise into catastrophic failings. By carefully evaluating welds, inspectors can validate adherence to make requirements and regulatory needs, therefore minimizing threats linked with architectural compromise.
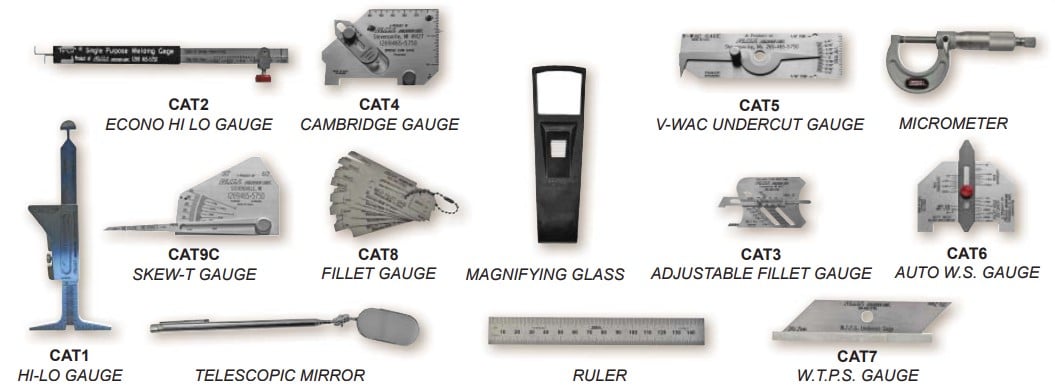
Moreover, efficient welding inspection improves the long life of elements, as it permits the very early detection of flaws that might result in degeneration over time. This aggressive approach not only extends the solution life of bonded frameworks however additionally advertises reliability and functional efficiency. In sectors such as building, aerospace, and automotive, where security is paramount, the evaluation process is important.
In addition, welding examination promotes a culture of top quality assurance within companies, encouraging adherence to best practices and continuous renovation. By investing in comprehensive evaluation protocols, firms can enhance their reputations and keep customer depend on. Inevitably, the relevance of welding examination lies in its capacity to support security, high quality, and long life in bonded structures, making it a basic part of design honesty.
Usual Welding Issues
A number of common welding problems can compromise the stability of welded frameworks, resulting in prospective failings if not dealt with. Amongst these defects, porosity is one of one of the most widespread, defined by the visibility of small gas pockets caught within the weld steel. This can dramatically deteriorate the joint, leading to reduced architectural honesty.

Another defect is insufficient fusion, which occurs when the weld metal falls short to sufficiently fuse with the base material or previous weld layers. This absence of bonding can produce weak factors that may fall short under anxiety. Likewise, absence of infiltration refers to insufficient deepness of weld steel, avoiding the joint from attaining its designated stamina.
Fractures can also establish throughout the welding procedure, frequently due to quick air conditioning or inappropriate welding parameters. These cracks might propagate under tons, resulting in disastrous failures. In addition, excessive spatter can inhibit the weld's high quality by presenting impurities.
Examination Methods and methods
Effective inspection methods and techniques are important for ensuring the integrity and durability of welded structures. A detailed inspection program utilizes a variety of non-destructive testing (NDT) approaches to spot possible issues without jeopardizing the welded elements. Among one of the most frequently utilized methods are visual examination, ultrasonic testing, radiographic testing, magnetic fragment screening, and color penetrant screening.
Aesthetic evaluation acts as the first line of protection, permitting assessors to identify surface area flaws such as splits, misalignments, or insufficient combination. Ultrasonic screening utilizes high-frequency acoustic waves to discover internal imperfections, giving thorough information concerning the material's integrity. Radiographic testing employs X-rays or gamma rays to picture the inner structure of welds, making it possible for the identification of voids and additions.
Magnetic bit testing is effective for detecting surface area and near-surface gaps in ferromagnetic products, while dye penetrant testing highlights surface-breaking issues using tinted dyes. Each approach has its one-of-a-kind benefits and limitations, necessitating a tactical combination to achieve comprehensive assessment insurance coverage. Implementing these strategies methodically guarantees that any kind of prospective problems are identified early, fostering the reliability and sturdiness of welded frameworks.
Effect On Architectural Honesty
The honesty of a framework is significantly affected by the quality of its welded joints, as they act as important points of strength and security. Poorly implemented welds can result in stress and anxiety concentrations, exhaustion failures, and ultimately, disastrous structural collapse. next The reliance on welding as a primary ways of signing up with materials demands strenuous examination methods to ensure that welds satisfy well established criteria and specs.
Shortages in weld top quality, such as incomplete blend, cracks, or porosity, can compromise the mechanical residential or commercial properties of the joint, impacting load-bearing capability and total efficiency. straight from the source When these flaws go unnoticed, they can circulate under functional tensions, resulting in a reduction in architectural integrity gradually. Thorough and normal inspections are essential in recognizing these weak points prior to they intensify into significant failures.
In addition, the effect of environmental elements, such as corrosion, can be worsened by poor welding techniques. Thus, making certain high-grade welding via alert evaluation not only advertises instant architectural dependability yet additionally expands the life span of components. Welding Inspection Milwaukee. Ultimately, the financial investment in proper welding inspection is a vital method for guarding versus architectural failings, therefore enhancing the longevity and safety and security of bonded structures

Best Practices for Effective Evaluation
Applying systematic inspection methods is important for making certain the honesty of bonded joints. Reliable evaluation begins with the growth of thorough checklists customized to the particular welding procedures and materials involved. These lists should include visual assessments, non-destructive testing (NDT) approaches, and documentation review to ensure that all aspects of the welding process are inspected.
Educating and accreditation of evaluation workers are critical parts of a successful evaluation program. Inspectors need to be fluent in different NDT strategies, consisting of ultrasonic, radiographic, and magnetic fragment screening, to properly determine flaws such as cracks, porosity, and insufficient blend.
Prompt examinations need to be set up at numerous phases of the welding procedure-- pre-weld, during welding, and post-weld-- to capture any prospective issues early. In addition, maintaining detailed records of inspections fosters accountability and facilitates future analyses.
Verdict
Welding examination is essential for determining defects additional hints and ensuring the stability of bonded structures. Eventually, effective welding evaluation not just safeguards structural integrity however additionally adds dramatically to the general dependability and sturdiness of welded joints.
Welding evaluation is an important part in the lifecycle of welded structures, serving as an aggressive step against possible failures that can endanger safety and security and performance.Welding inspection serves as an important safeguard in the stability of welded structures, making sure that they satisfy strict safety and top quality requirements. Welding Inspection Milwaukee. Ultimately, the value of welding evaluation lies in its capability to copyright security, quality, and longevity in bonded frameworks, making it an essential element of engineering integrity
Ultimately, the investment in proper welding evaluation is a vital approach for securing versus architectural failings, therefore improving the durability and safety and security of bonded structures.
Welding inspection is crucial for recognizing flaws and ensuring the integrity of welded frameworks. Welding Inspection Milwaukee.